Results of the project
The system developed by Yeditek completely eliminated occupational safety risks and achieved 100% success in error detection.
Despite the variability in the process, visual inspection was successfully carried out, ensuring high reliability under all production conditions.
The system established an effective control mechanism within the cycle time without altering the existing line flow.
This automated system, which replaced manual inspection by visually monitoring and manually continuing the line, automated the manual processes.
With the reduction in approval time in operations, it significantly increased line efficiency.
This innovative solution was selected as a best practice in the automotive sector and served as an example across the industry.
Challenge
TOFAŞ was facing difficulties in verifying whether vehicle bodies were properly placed on the carrier skids on the production line. The existing manual control methods were time-consuming and adversely affecting production efficiency and occupational safety due to incorrect placements.
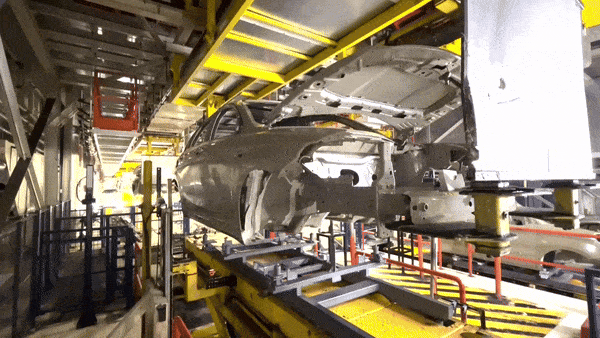
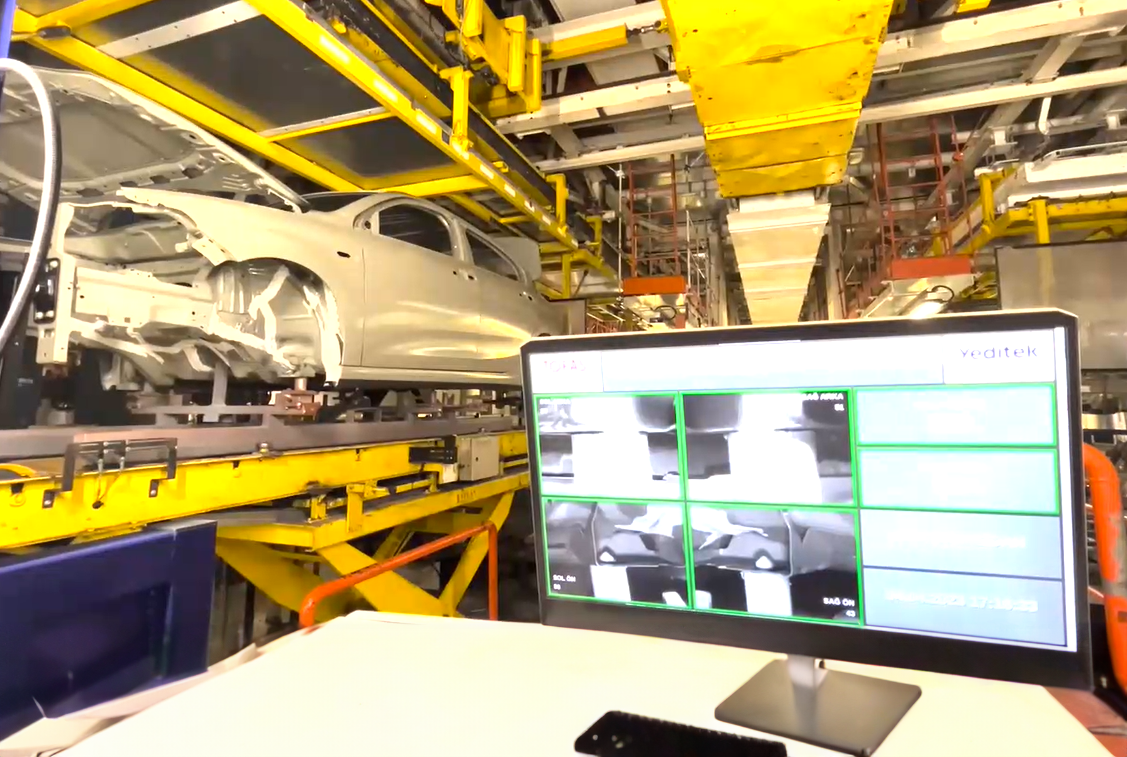
Solution
Yeditek developed a custom automatic visual inspection system for TOFAŞ, capable of verifying the correct placement of vehicle bodies on the carrier skids with 100% accuracy on the production line. This system eliminated occupational safety risks and effectively provided visual inspection despite process variability. It significantly increased process efficiency by operating within the cycle time without altering the existing line flow.